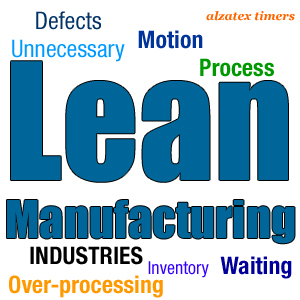
Because of the increasing pressure from customers and competition to reduce costs in the current recession, many companies want to begin lean implementation. Like any other major change, effective lean implementation steps begin with a good plan. Learning what it takes to go lean can be one of the largest steps any company can take to improve efficiency and over all performance of your organization. The number of companies that are going lean are increasing daily. With the current nature of the world wide economy it is easy to understand why. Let’s look at some lean implementation steps that can help in this process.
1. Perform An Initial Lean Assessment. The purpose of a lean implementation assessment is to identify organizational strengths and weaknesses and determine how lean your organization is initially in your different areas. It should include financial and operational analysis. It is important to select an employee or consultant with significant lean experience to conduct the assessment. While someone internally might have the necessary experience, an outsider might help to provide a new perspective that can prove to be very beneficial in the planning stage. It can also help in convincing members of the management team that might not initially be on board with the change.
2. Begin tracking metrics. The lean assessment will provide the baseline and answer the question of where are we as a company? Tracking and posting metrics will show you where you are going during the lean transformation and will gauge how successful your lean implementation steps will be. Develop a set of metrics that you will use to track your implementation efforts. It is important to select a reasonably small number of metrics and post them in the plant. Metrics should not be reserved for management’s eyes only, they need to be transparent and available for everyone to see.
3. Develop a one year detailed implementation plan and three to five year plan as well. Based on the lean assessment and metrics selected, develop a timeline for your lean implementation steps. It should include goals and milestones. The plan needs to be tailored to the unique circumstances of the organization. Not every plan will look alike.
4. Also, develop a training plan. Companies commonly make two mistakes with regards to lean training. Either they train too much too early or they fail to train at all. Both of these mistakes can prove to be very costly. It is important to develop a training plan that coincides with the implementation plan. You should identify who should be trained, when they should be trained, and in what disciplines they should be trained for your lean implementation steps to go smoothly.
5. Develop a communication and performance reward plan. Communicating the plan to go lean to everyone in the organization and letting them know how this will effect them is critical to your success. Part of the communication plan should include a plan to reward both teams and individuals for their successful participation in your lean implementation steps.
As you plan your lean implementation steps in the future, keep these five keys in mind. They will help you to move more quickly toward successful implementation. Alzatex Lean Manufacturing Timers are an excellent tool to consider. Contact Alzatex for more information.